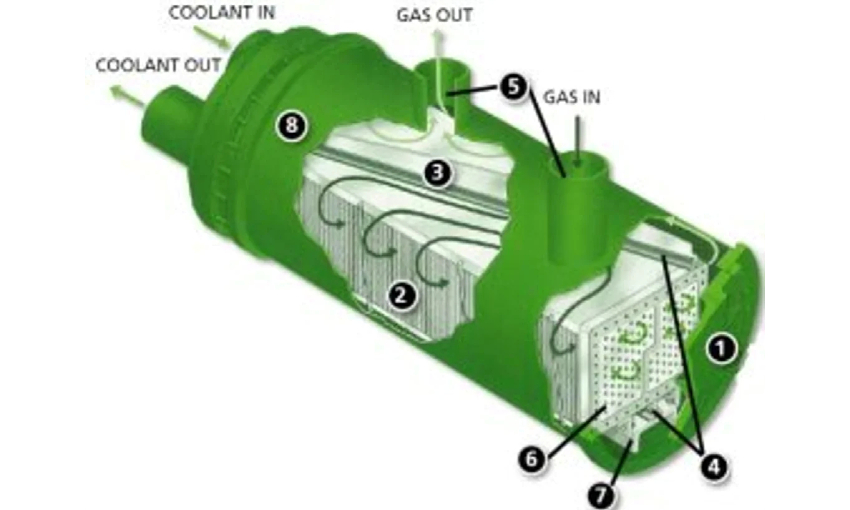
Discover the key components that ensure your air compressor operates efficiently and maintains peak performance. This article delves into the importance of air compressor coolers, specifically aftercoolers, intercoolers, and oil coolers. Understanding their functions and types will empower you to make informed decisions for your industrial air compressor needs.
Air compressor coolers, including compressor intercoolers, aftercoolers, and oil coolers, are essential heat exchangers designed to regulate temperature and moisture levels in compressed air. Their multifaceted roles contribute to higher compression ratios, reduced moisture content, protection of downstream equipment, and the maintenance of optimal operating conditions.
An intercooler plays a crucial role in reducing scheduled maintenance for both the compressor and downstream air tools. It prevents corrosion in various types of compressors, including reciprocating, rotary screw, and centrifugal compressors. This results in extended equipment lifespan and efficient compressed air piping systems.
Compressed air discharged from a compressor carries high temperatures, posing challenges for lubrication and causing moisture-related issues. Elevated temperatures can lead to material degradation and compromised performance. Compressor coolers, such as intercoolers and aftercoolers, address these concerns by reducing the temperature of compressed air, preventing rust, scale build-up, and maintaining an optimal dew point.
Our advanced manufacturing technology ensures the production of high-quality air coolers, including intercoolers and aftercoolers. Adhering to OEM "donut-type" designs, our coolers provide a perfect balance between pressure loss and CTD values. With a standard warranty of eighteen months, our Turbo-Air® air coolers guarantee interchangeability and at least comparable performance to OEM products.
Our Turbo-Air® Intercoolers offer an optimal balance between pressure loss and performance values, ensuring 100% interchangeability for Cameron Turbo air 3000 and MSG Compressor. Manufactured to the highest standards, these coolers come with a standard warranty of eighteen months, emphasizing our commitment to delivering top-quality products.
Choosing the right air compressor cooler is crucial for ensuring the long-term efficiency and reliability of your compressor. Whether you opt for air-cooled or water-cooled solutions, understanding the functions and advantages of each type will empower you to make informed decisions that positively impact your industrial air compressor's performance.
Ready for unparalleled service?
Click here now to connect with us
and experience exceptional customer support!